Industrial 3D Printing and its Benefits to Product Design and Manufacturing
In 3D printing or additive manufacturing as the industrial 3D printing’s official term is, a physical object is manufactured from a digital 3D model with a 3D printer. The biggest difference to the traditional manufacturing methods, where an object is usually produced by removing material, is that in 3D printing the product is created by adding material layer by layer. The principle is always the same regardless of the printing technology or material.
3D printing is not applicable in all cases, but when it is, compared to traditional manufacturing methods, 3D printing has many benefits that can open up and enable new business opportunities and more operational efficiency:
- The product portfolio is kept in digital storage and the physical products are manufactured only against customer demand, which gives an opportunity to offer a much wider range of for example spare parts and keep them available longer creating new high-margin revenue. Also, this enables product design to be easier repairable and hence supports the circular economy as well as sustainability.
- More freedom of design when even the complex shapes and functional assemblies can be printed as one piece.
- The design can be optimized for functionality instead of manufacturability, which leads also to an optimized shape and material consumption.
- Faster product development time when the prototypes and test products can be manufactured and changes to the design made within days.
- No need for tooling so production and sales can start faster. Also, changes during the product life cycle are fast and easy to implement and the product’s end of life is easier to manage.
- Production can be on-demand only, stocking is not necessary.
- Cost-efficient production of single pieces and small series.
- Producing customized products including mass customization almost without added costs.
- Production generates very little material waste.
- Cost-efficient logistics and supply chain, especially when 3D printed locally near the customer.
- Also, traditional manufacturing processes and production lines can be made more efficient by integrating 3D printing solutions to applicable phases.
We 3D print end products and prototypes both single pieces and series like components, partial and functional assemblies, spare parts, production tools, scale models, and many others. Contact us and ask for a quote.

Printing Technologies
New 3D-printing technics are created all the time, but usually, technologies are divided into seven main technologies, which are then further split into several sub-technologies. HP Multi Jet Fusion printers are used in our in-house production, but thanks to our extensive sub-contractor and partner network we are able to provide prints in most printing technologies and available materials including metal prints. Short introductions of the most common printing technologies are given below.
HP Multi Jet Fusion (MJF)
The heart and soul of our in-house production are two HP Multi Jet Fusion 4200 3D printers. Multi Jet Fusion (MJF) technology, developed by HP, is one of the fastest and most cost-efficient industrial printing technologies on the market. MJF is based on powder bed fusion, where the objects are made of powder by fusing and curing it with the help of heat and agents. A full height build is printed in ca. 16 hours and the cooling time is ca. 2 days. This is for the maximum height and the lower the build the faster it is printed and cooled. There is also a fast cooling option that shortens the cooling time significantly. However, not all objects are suitable for fast cooling so whether the fast cooling can be applied to the build must be checked and decided case by case.
We have in our inhouse material portfolio two different options, HP High Reusability PA12, and now also HP High Reusability PA12 Glass Beads, that is ideal for applications that require more stiffness.
MJF suits very well for printing functional products and complex high precision designs, both quality end products, and prototypes. The prints can be post-processed by painting, dyeing, or varnishing them. There are very few design limitations, but since the powder works also as support, its removal must be taken into account in the product design. Find more design tips from the attached document.
The volume of the printing chamber: 380 x 284 x 380 mm
Printing speed: 4000 cm³/h (full chamber ca. 16h)
Layer thickness: 0.07-0.1 mm
Material: PA12 (polyamide), PA12 Glass Beads (polyamide with 40% of glass beads)
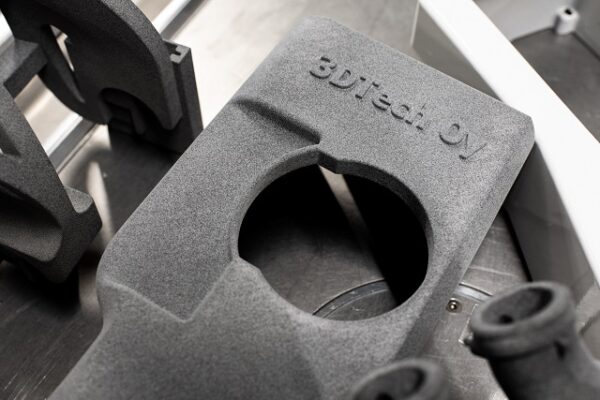
Fused Deposition Modeling (FDM)
For many people, Fused Deposition Modeling (FDM) is the most familiar 3D printing technology since the affordable desktop printers that are used for example in schools and by hobbyists are mainly based on FDM technology. In FDM, the filament is melted and then extruded onto the printing bed layer by layer. The material cures as it cools. Above mentioned affordable FDM printing should not be mixed with the industrial FDM printing that is from the quality and pricing point of view at a very different level.
At our facility, we provide filament printing services using the Markforged Onyx One printer. The Onyx One is a 3D printer based on Fused Filament Fabrication (FFF) technology, which produces high-quality and durable parts. The material used is Onyx, a nylon reinforced with finely chopped carbon fiber. This blend enhances the strength of the printed parts, ensures excellent dimensional accuracy, and reduces or eliminates the warping often associated with 3D prints.
3D printing with strong materials opens up various possibilities for production and product development, offering a quick and easy way to create robust and functional prototypes for rigorous testing.
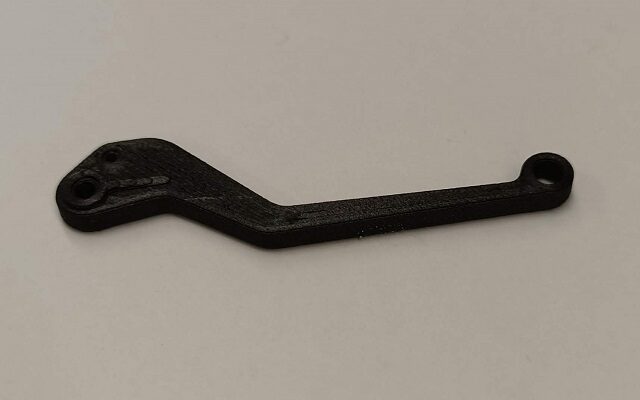
Stereolithography (SLA)
Stereolithography (SLA) is one of the oldest 3D printing technologies. In SLA, the object is made of liquid resin by curing it with a laser. It is possible to produce both soft and hard objects and it suits very well for prototypes of relatively small products that have high precision details, statues, jewelry and molds that require a smooth surface. The support structure is built of the same resin material and is removed mechanically. The prints can be post-processed for example by painting or varnishing them.

Selective Laser Sintering (SLS)
Selective Laser Sintering (SLS) is one of the most common industrial 3D printing technologies. SLS is a powder bed-based technology, where the powder is sintered with a laser. The material is usually polyamide, although some elastomers have recently become available, too. In SLS the printing speed is relatively fast, but the cooling time rather long.
There are very few design limitations and the technology is suitable for printing functional products and complex designs of end products and prototypes. The powder works also as a support material and its removal must be taken into account in product design. Overall, the surface quality and other features and similar to objects printed with HP MJF technology. There are a couple of significant differences, though. SLS prints are white whereas MJF prints are grey. MJF prints have also a higher density. Thanks to the white color dyeing of SLS is easy and the variety of colors wide.
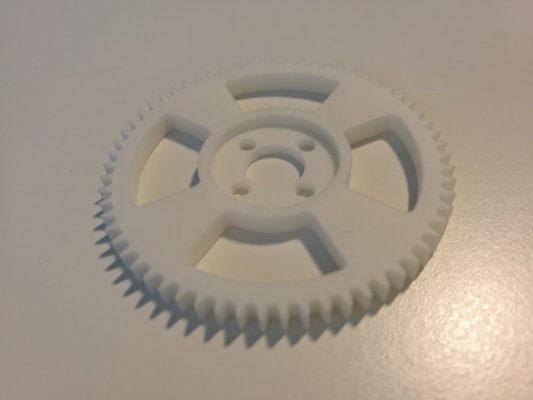
Metal Printing
Metal printing is currently the fastest growing area in the 3D printing industry globally. It has two common technologies, Selective Laser Melting (SLM) and Electron Beam Melting (EBM). Both technologies are based on the use of heat for melting the metal powder, in SLM with laser and in EBM with electron beams. Both of them require a support structure that works also as heat conductors. There is a wide variety of available metal materials aluminum and steel being the most commonly used.
The quality of the metal prints is equal to products manufactured with traditional methods with regards to chemical compounds, mechanical features as well as microstructure. Printed objects can and basically almost always should be designed so that they are optimized for their functionality, which enables smaller and lighter solutions. This is one of the reasons why especially aircraft and vehicle industries are increasingly implementing 3D printing in their processes. The wider implementation across different industries has been slowed down by the higher cost of metal printing compared with plastic printing, which is mainly due to more expensive equipment and material, but especially due to the demanding and labor-intensive post-processing of the prints. Also, product designers are required to have a whole new approach and skillsets when they design products for metal printing. When considering whether a metal product should be 3D printed or manufactured with a traditional method like CNC machining, there is a thumb rule to follow. If the product is possible to be manufactured with a traditional method, it very rarely is feasible to be 3D printed without redesigning it so that it is optimized for 3D printing.
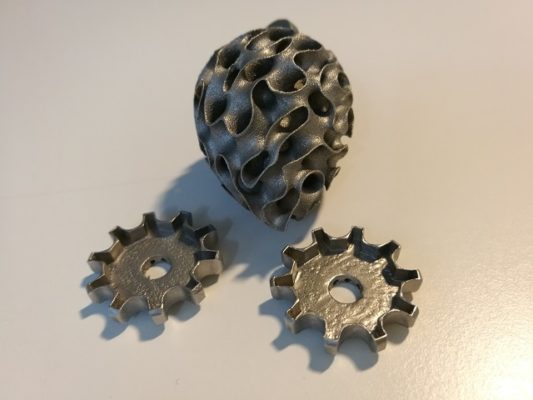
Additional Services
As an additional service, we offer post-processing of printed objects.
Dyeing is the most commonly asked post-processing service. In dyeing, the objects are sunk into a dye that is absorbed into the object. This method does not impact the measurements, surface quality, or other features of the object. HP MJF prints are naturally grey on the surface and black inside, which limits the number of available dyeing colors. At the moment black is the only option. For SLS prints, there are more color options.
We paint/varnish single products and a series of few pieces also ourselves, but usually, in case of bigger batches and more demanding needs always, we use a professional paint shop. This service is available for all plastic prints.
We offer also selected special coatings for prints like nano-coating, and as a new service, ESD-protection. We perform also various assembly work, attach screw inserts, etc.
Contact us and ask more about the additional services.
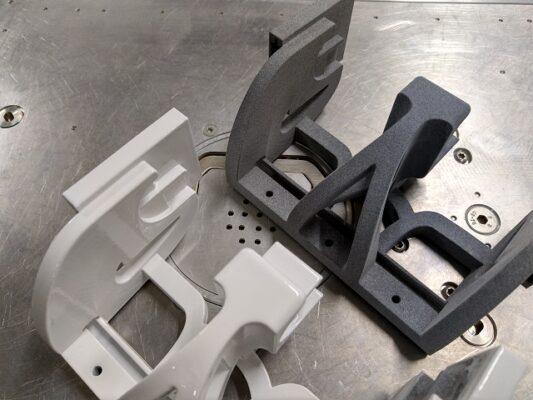